Video Library
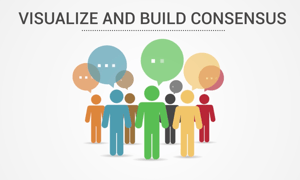
Discover the four categories of improvement tools: visualization and consensus building, understanding requirements, problem solving techniques, and data analysis
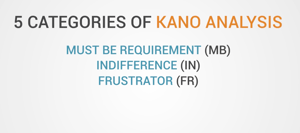
Unlock the power of KANO analysis in your projects! This segment breaks down how to categorize requirements into must-be and delighter features, helping you prioritize what truly matters to your customers. Elevate your project management skills with this essential tool!
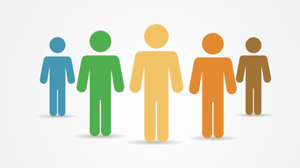
Discover the crucial steps in identifying customers for your projects! Understanding the diverse expectations of stakeholders can prevent unintended consequences and improve outcomes. Tune in to learn how to effectively recognize and engage with your customers!
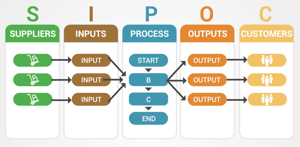
In this video, you'll learn how to use the SIPOC tool to map out any process by identifying key Suppliers, Inputs, Process steps, Outputs, and Customers.
It’s a powerful way to clarify scope, align your team, and build a solid foundation for improvement.
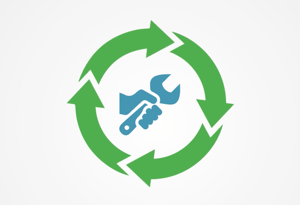
In this video, you’ll learn about the eight categories of waste commonly seen in processes—summarized by the acronym DOWNTIME—and how to recognize them in both manufacturing and transactional environments. You’ll gain insights into identifying and reducing these wastes to improve productivity, reduce costs, and create more efficient workflows.
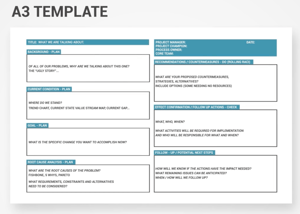
Dive into the structured categories of the A3 tool! From background to root cause analysis, each section plays a crucial role in understanding and addressing project challenges. Stay focused on the problem and pave the way for effective solutions.
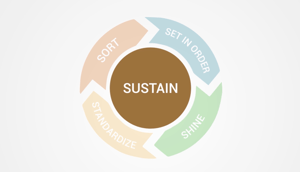
In this video, you’ll learn the 5 essential steps of the 5S system—Sort, Set in Order, Shine, Standardize, and Sustain—and how they work together to eliminate waste, improve productivity, and build a strong foundation for continuous improvement.
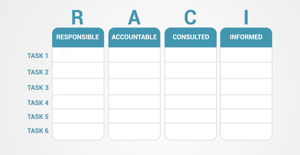
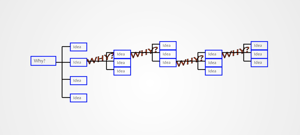
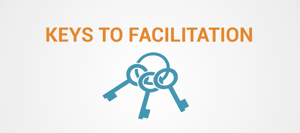
In this video, you'll learn the key attributes of effective facilitation—from creating collaborative environments and structured group processes to driving engagement, guiding outcomes, and modeling professionalism. These core skills will help you lead productive sessions and support successful team collaboration.
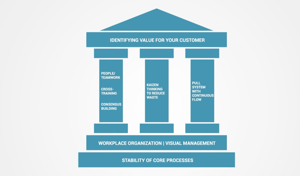
This video provides an overview of Lean as a system and its five core principles: Defining Customer Value, Mapping the Value Stream, Creating Flow, Enabling Pull, and Striving for Perfection.
What You Will Learn:
You’ll learn how Lean helps identify and eliminate waste, how tools like 5S, visual management, and Kanban support continuous improvement, and how the system emphasizes teamwork, standardization, and customer-focused value delivery.
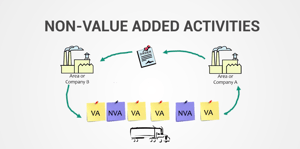
In this video, you'll learn how to define and scope a successful improvement project by focusing on observable waste, achievable timelines, and strong stakeholder support. You'll also explore the difference between projects and rapid Kaizen events—and understand when to use each approach for maximum impact.
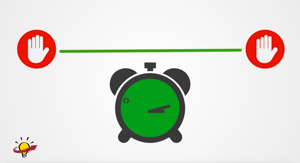